
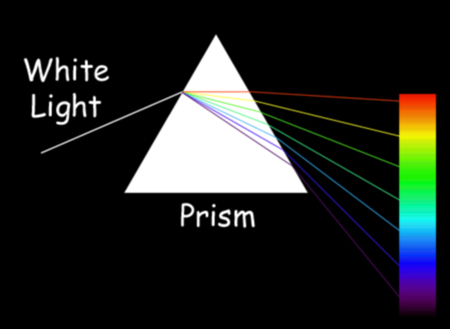
In this fourth stage, the edges of the prism are subjected to a spinning diamond plate in order to slightly dull the sharp edges it obtains throughout the aforementioned steps (Figure 2d). Once polishing is completed, chamfering can begin.
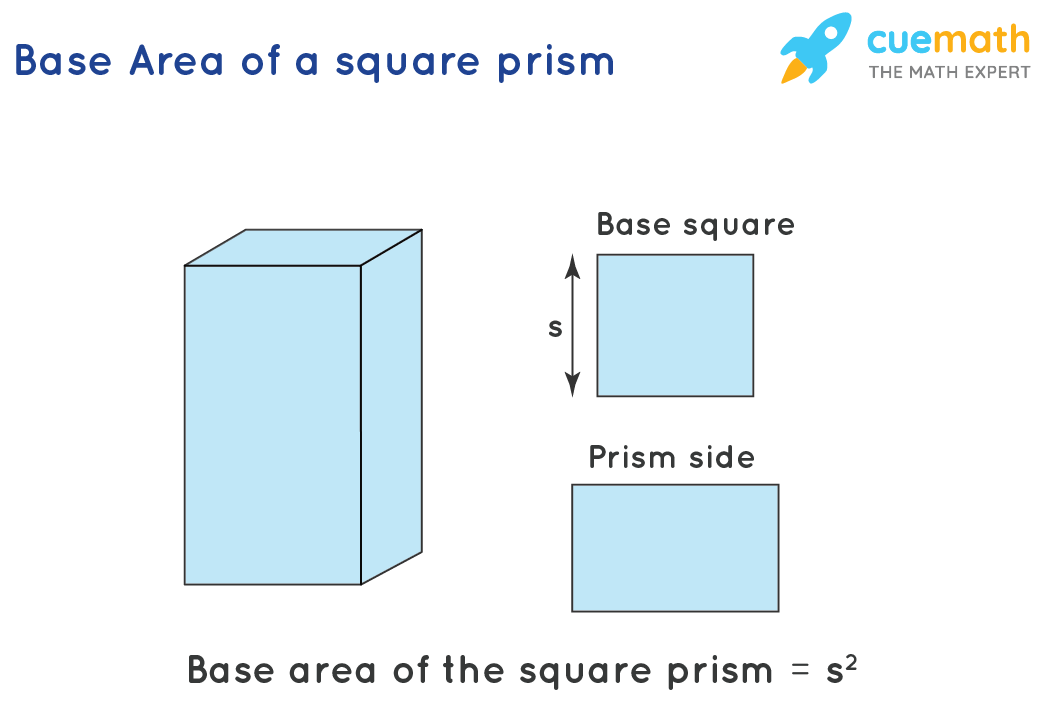
The exact duration of the polishing stage is highly dependent on the surface specifications required. In this stage, the glass is rubbed against a polyurethane polisher wet with "slurry," an optical polishing compound typically comprised of water mixed with pumice or cerium oxide (Figure 2c). The third stage involves polishing the prism to the correctly specified surface flatness. In both the first two stages, the prism surface must be wet in order to expedite glass removal and prevent overheating of the glass itself. After smoothening, the glass surfaces should appear cloudy and opaque. Scratches left from the first stage are removed in the second stage (Figure 2b). Next is a fine grinding process that removes sub-surface breaks from the surface this stage is known as smoothening. At this point, the dimensions of the prism-to-be are very close to the desired specifications. A majority of the glass is removed quickly in this stage resulting in flat, but still coarse surfaces (Figure 2a). This block is then ground, or generated, by a metal diamond bonded wheel into a near-finished product. In addition, most high precision prisms tend to be made in low quantities, meaning an automated process would be unnecessary.įirst, a block of glass (known as a "blank") of a specified grade and glass type is obtained.
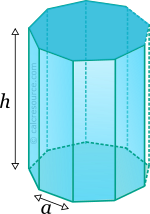
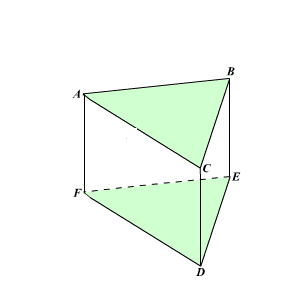
Due to the variability in shape, size, and, most importantly, the number of surfaces, a large-scale automated process for prism manufacturing is quite infeasible. In order to be used successfully in most applications, prisms must be manufactured with very strict tolerances and accuracies. PRISM MANUFACTURINGīefore delving into the theory behind prisms, consider their manufacturing process. Therefore, the substitution of one prism in lieu of several mirrors reduces potential alignment errors, increasing accuracy and minimizing the size and complexity of a system. Often, multiple mirrors are needed to achieve results similar to a single prism. Replacing mirror assemblies is perhaps the most useful application of prisms, since they both bend or fold light and change image parity. A notable characteristic of prisms is their ability to be modeled as a system of plane mirrors in order to simulate the reflection of light within the prism medium.
